Using its precision manufacturing techology, MAP Plastics is riding on the growth in Singapore’s burgeoning biomedical sciences sector.
Last year, Singapore’s bio-medical manufacturing output increased 11.5% year-on-year.
Singapore’s medical technology manufacturing output in 2008 was close to S$3 billion, and the Economic Development Board is targeting to increase this to S$5 billion by 2015.
Strong demand is why capacity utilization at MAP Plastics is as high as 85% even after its latest million-dollar clean room was completed in December last year.
The Singapore operation now operates a total of 57 injection moulding machines, and designs and fabricates about 150 molds a year.
Its operations in Suzhou serves mobile phone, display optics and electronic industries, but the focus is changing to the biomedical sector.
The trend of manufacturers moving to China to cut cost is reversing: there are those moving factories back to Singapore, according to the managing director of MAP Plastics, Mr Loy Chit See, when NextInsight visited the factory.
These are usually high tech companies who have encountered difficulties in China in protecting their intellectual property rights and quality.
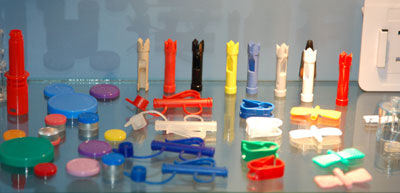
Global leaders that have set up manufacturing, R&D and headquarters function in Singapore include Applied Biosystems (AB), Affymetrix, Alcon, Baxter International, Becton Dickinson, Bio-Rad, Ciba Vision, Thermo Fisher Scientific, Fluidigm, Edwards Lifesciences, Hoya Healthcare, Hill-Rom, Illumina, Qiagen, Japan Medical Supply (JMS), Medtronic and Siemens Medical Instruments.
Other component makers that support both consumer electronics that are also supporting the medical sector, include Fischer Tech, Beyonics and Medtecs.
MAP Plastics was part of a stable of plastic injection-molding factories bought by MAP Technology in Aug 2008 as part of its strategy to diversify out of precision stamping and die cutting for the HDD sector.
Unlike the cyclical consumer electronics industry, the medical device sector is highly defensive and stable, said Mr Tommy Ong, senior manager of MAP Plastics.
Product life cycle is extremely long – as high as 20 to 30 years. This is due to the high reliance by physicians on data documenting the efficacy of a specific medical device.
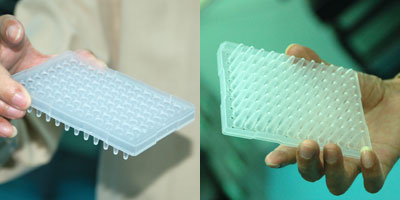
In contrast, the life cycle of consumer electronic gadgets such as hand phones could be as short as 12-18 months.
Other than diversification, the plastic injection-molding business is also better margin-wise – FY08 margins were 16.5%, compared to consolidated segment margins of 7.7%, according to MAP's annual report.
MAP Plastics contributed $14 million in revenues for FY09, or 9% of the group's revenue.
MAP Tech generated group revenues of US$157.2 million for FY09 and a net loss of US$24.3 million.
The loss arose mainly from once-off matters such as an impairment of goodwill when it closed down a factory in Malaysia (making components for printers) from its plastic injection molding acquisition.
Related story: BROADWAY, MAP, etc: HDD recovery to benefit component makers