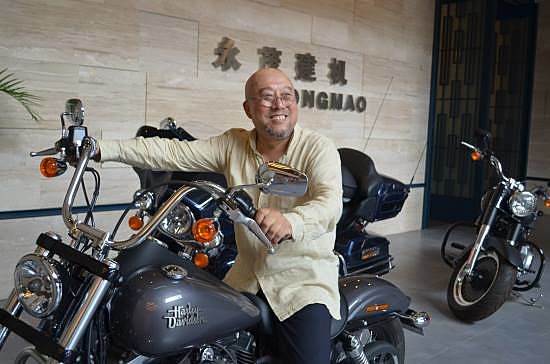
Visuals by Sim Kih unless otherwise indicated.
In this second report from NextInsight's visit to Yongmao's crane facility in China, we gain insights to the X-factor behind world class manufacturing. For our first report on the company's strategy and market position, click here.
WE WERE shown the facility grounds by Yongmao's founder and executive chairman Sun Zhaolin, whose corporate philosophy is: "A cultured team is a winning team."
He had worked with local universities to design the facility that we visited.
The facility is relatively new, having commenced operations in September 2012.
Video: Yongmao's facility in Fushun, Liaoning, China | |
That could be why it was extremely clean, highly automated and modern - It is the best tower crane plant in China, according to the executive chairman.
It also has its own R&D center that has developed about 60 models and sub-models of tower cranes.
Costing Rmb 220 million, Yongmao's Fushun facility occupies sprawling grounds of 240,000 square meters - the area of 30 soccer fields.
The building and equipment had cost Rmb 200 million, while land use rights for 60 years (expiring in 2063) cost Rmb 20 million.
CFO Yap Soon Yong has estimated the piece of land in Fushun to be worth Rmb 60 million to Rmb 80 million currently.
As Yongmao has its roots as a crane parts manufacturer, the visiting delegation from Singapore was able to observe how cranes were built from scratch using raw steel plates.
(Yongmao started as a distributor of construction materials and metal casing parts in 1992. In 1996, it went into the manufacturing of construction equipment accessories such as towercrane mast sections, tie collars and fixing angles. In 1998, the company commercialized the first tower crane that it designed. In the early 2000s, it became China's first company to export tower cranes.)
The crane parts that it made were so good that its products were exported to Southeast Asia. Then, customers began asking if Yongmao could manufacture entire cranes.
Today, the company manufactures more than half of the parts used in a Yongmao crane by cutting, machining and fabricating steel plates.
The other parts such as the operator cabin and slewing mechanism are procured for assembly at the client's construction site.
The best equipment
Reporters and an investment analyst from Singapore checked out Yongmao's cutting and machining facility in Fushun, Liaoning, China.
All welded components are shot blasted for stress relief to ensure long life weld joints.
They are then treated with a layer of zinc metalising coating as an undercoat, followed by epoxy paint coating and thereafter oven baked to the required specifications.
Crane modules are painted before being packed into containers for shipment to the customer's construction site. Each crane easily takes up 10 to 12 containers.
It typically takes 30 to 45 days to build a crane from scratch.
However, it can take up to 2 months to make a customized crane.
Customers sometimes pay for design customization due to requirements that could arise from a myriad of reasons ranging from construction site constraints to lift loads.
Sante, one of its largest customers in Singapore, is one customer that wants all their parts tagged.
Yongmao's gigantic luffing crane comes with an 80-meter bib arm. A 20-storey HDB block is about 80 meters in height. Photo by Sun Zhaolin
People are its best assets Yongmao's welders have a reputation of being the best in China. They are recruited from local technical colleges and undergo further training in-house.
Staff training is an integral part of Yongmao's corporate culture. It staff training programmes include induction training, on-going training and external training.
"From our experience, it is entirely plausible for China to train and produce workers as good as those in developed countries," said the CFO.
Tower crane experts are also invited to train Yongmao's production workers in the latest technical know-how.
There are currently about 600 production workers and 300 white-collar staff working at its Fushun facility, plus another 600 people at its facility in Beijing.
Its human development programmes include the following.
New employees
Induction training to equip new employees with the necessary skills for their jobs, familiarise themselves with corporate culture, company regulations and policies, existing and new products as well as manufacturing and safety regulations.
After the induction training, all new employees are required to sit and pass an examination which includes a practical assessment.
Existing production workers
- Certification courses organised by government-appointed training centres where they receive training on production and safety procedures as well as specialised technical knowledge and skills.
- Sent to university and polytechnic for further technical training
Senior executives, middle management and supervisory staff receive training classes according to job scope.Customers love Yongmao's intricately bound crane catalogue with product specifications. This is not a marketing gimmick - Yongmao's dedication to its corporate culture of excellent workmanship extends to every tiny detail.
Many thanks to the Yongmao management for hosting us!
Recent story: YONGMAO, SIN HENG, TAT HONG: Which Crane Player To Bet On?