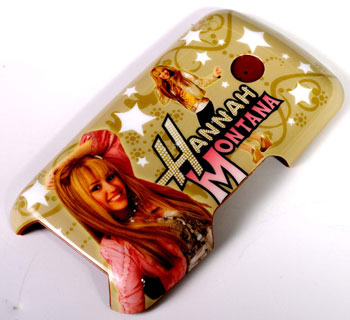
SLEEK DESIGNS and high-color fastness are what gadget makers use to visually cajole consumers into parting their premium dollar for latest technology upgrades.
A plastic-injection-molding manufacturer has edged its way into being part of the marketing value chain for consumer electronics giants.
Using “in-mold decoration” or IMD technology, China Kunda (9 Oct IPO: 21.5 cents) embosses gorgeous graphic designs in a film of hard coat on plastic casings of consumer electronic gadgets.
Kunda’s IMD technology is applicable to just about any tech gadget, and end products have ranged from Motorola's mobile phone casing to Sanyo’s bread maker panels.
”Unlike traditional spray-painted plastic casings which easily show visible signs of wear and tear within a year of use, IMD casing have life-long durability,” said Kunda CEO Cai Kaoqun during an exclusive interview with NextInsight.
Kunda’s factory gate price for an IMD mobile phone case could be as high as Rmb 15, several times that of a traditional spray-painted case, revealed the CEO.
IMD has a wide application, and is currently used by big-name consumer electronics manufacturers to differentiate their high-end models.
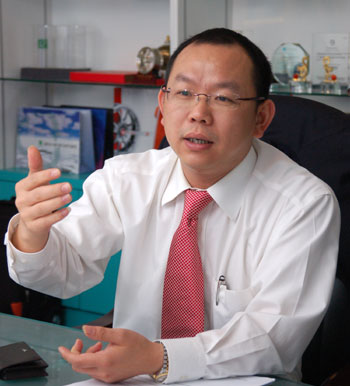
IMD casing is also abrasion and chemical resistant and therefore environmentally safer, a boon to consumers wary of health hazards associated with the peeling of spray-painted parts.
Sub-contract manufacturing of IMD precision plastic parts is the most lucrative of Kunda’s three business segments, the other two being
(1) Design and manufacture of moulds used by plastic auto-parts makers; and
(2) Production of plastic injection parts
IMD is a complex process requiring technical aspects of various crafts ranging from silk-screen printing, cutting and forming, right down to plastic injection molding.
In China, reliable supply of quality IMD is scarce, making it a lucrative business – for the first nine months of FY08, Kunda’s gross margins for IMD were as high as 45%.
However, Kunda’s strongest earnings driver is currently its mold design segment, which contributed 78% of its gross profits in the first nine months of FY08.
Mold demand drivers
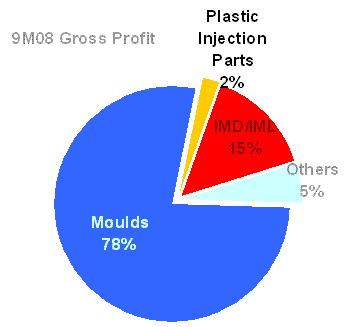
Kunda designs and makes high-precision molds mainly used in automobiles, electronics and electrical appliances.
Plastics are used in most electronic devices and most plastic components on the market today are injection molded.
Automobile molds contributed 46% to Kunda’s first nine months of FY08 mold revenues. It has designed and made molds for automobile models from Audi, BMW, Chrysler, Ford, Fiat, Isuzu, Mitsubishi, Volkswagen and Volvo.
Three factors drive demand for Kunda’s auto parts molds:
(1) Robust automobile demand
Despite the credit crunch, China’s automobile demand is still expected to grow about 10% in 2008, according to China Association of Automobile Manufacturers.
95% of auto parts in China are manufactured using molds. In fact, one single automobile model usually requires as many as 4,000 sets of molds!
(2) Substitution of steel auto parts with plastic injection parts
Secondly, the 4,000 ballpark figure is set to increase, as the auto industry is trending toward replacing steel parts with plastic injection parts.
The management cites 3 advantages of plastic injection auto parts: lightweight, improved fuel efficiency, and environmental friendliness.
(3) Import Substitution
Other than a growing end user market, Mr Cai also expects to gain market share from foreign mold makers.
China imports half of its mid to high end molds, according to a June 2007 report by Forward Intelligence on its die and mould industry.
These include the high-precision molds designed and produced by Kunda for the automobile industry, which it makes available to auto parts makers for a third of import prices or less.
Kunda’s ability to compete with foreign mold makers on cost is a third reason why Mr Cai is upbeat about the company’s prospects.
”Mold design and manufacturing is a technically complex job, which is why it is much more lucrative than just mass-producing the plastic injection parts,” says Mr Cai.
An injection molded plastic part is created using an injection-molding machine, which works by melting plastic pellets, and injecting them into a mold.
”It is technology-intensive, capital-intensive, requires the use of highly skilled labor and complex factory management,” he adds.
In the first nine months of FY08, Kunda’s gross margins were 39% for mold design and manufacture, compared with a mere 3% for making plastic injection parts.